Material: 1.2/1.5/2.0 mm Thickness
The 1.5 mm thickness raw material for inspection, in common use
Ex Cold Rolled Coil, Galvanized Coil, Yield strength: 250Mpa
The profile would be double check.
Machine Components
Uncoiler Straightener &NC feeder 3in1 Machine

Standard accessories and features:
1) Straightener adjustment adopts Dial indicator
2) Width adjustment is controlled by fast handwheel
3) Pass line height is adjusted by lifter driven by handwheel
4) Uncoiler with 4 ‘A’ coil retainers
5) Pinch roll and straightener roll adopts high strength alloy bearing steel, with hard chrome plating.
6) Pneumatic hold down arm device.
7) The feeding system is controlled by Mitsubishi PLC
8) Feed accuracy is controlled by servo motor from YASKAWA with precise planetary reducer.
Specifications:
1) Applied material width: 75-300mm
2) Material thickness: 0.3mm-2.3mm
Thickness
|
0.3-1.3mm
|
1.8mm
|
2.3mm
|
Max feed width
|
300mm
|
230mm
|
180mm
|
3) Max coil weight: ≤1000kg
4) Coil inner diameter: 508mm
5) Coil outer diameter: ≤1000mm
6) Speed: max 16M/min
7) Feed pitch accuracy:±0.15mm
8) Feed roll: Upper 1 / Lower
9) Straightening roll: Upper 4 /Lower 3
10)Air power supply: 5kg/cm2
11)Decoiling mandrel expansion: manual
12)Servo Motor:AC1.8KW
13)Decoiling Motor:AC0.75KW
Hydraulic Pre-Punching device
Feeding rollers with guide section
Hydraulic pre-shear only for cut off the head of first piece and tail of end piece
Two steps of Powered feeding rollers, driven by SERVO MOTOR
Total TWO units of punching station to punch holes in the middle of the bottom
1st Punching station, for punching 1-9X29 hole
2nd punching station, for punching 1-9X13

Hydraulic group, Pump motor: 18.5KW
Cold Rolling Mills
The feeding section with guide
Gear/Sprocket driving, 14 stages to form
New frame stand design
Rollers manufactured from Cr12MoV, CNC lathes, heat treatment, Nitrided
Shaft Diameter=Φ75mm, Precision Machined
Main Motor=7.5KW, frequency speed control
Max. line speed of roll former: approx. 12m/min(exclude punching time)
Straightening device
The following picture is for your reference only
Hydraulic Cutting device
Stop to Cutting, Post Cut, slug breaker
Cutting tool material: Cr12, Heat treatment
Share in the same hydraulic group with pre-punching device
PLC Control System
Control the quantity &punching length& cutting length automatically
Combined with: PLC, Touch Screen, Inverter,
Encoder, etc
Cut-to-length tolerance≤±2 mm
Control Voltage 24V
Product rack Un-powered, 4 meters long
OPTION 1: Specification of TNCF2-300 Uncoiler Straightener &NC feeder 3in1 Machine
Standard accessories and features:
1) Electric eye loop control system.
2) Feed line height easily adjusted by advance worm gear screw jacks device.
3) Feed and Straightening rolls coated with hard chrome.
4) Hydraulic hold down arm with motorized wheel
5) Transformer
6) PLC control feeding program from Mitsubishi.
7) Side guider
8) Compact design, minimum space required,
9) Hand-wheel-adjusted coil width guides
10) Pendant controls
11) Uncoiler mandrel Expansion is Hydraulic with coil support, Also to avoid sheet came out from the coil during running, 'A' type coil retainer mechanism is used.
Specifications:
1) Applied material width: 75-300mm
2) Material thickness: 0.3mm-2.3mm
Thickness
|
0.3-1.3mm
|
1.8mm
|
2.3mm
|
Feed width
|
300mm
|
230mm
|
180mm
|
3) Max coil weight: ≤2000kg
4) Coil inner diameter: 508mm
5) Coil outer diameter: ≤1200mm
6) Speed: max 16M/min
7) Feed pitch accuracy:±0.15mm
8) Feed roll: Upper 1 / Lower 1
9) Straightening roll: Upper 5 / Lower 4
10)Air power supply:5kg/cm2
11) Decoiling mandrel expansion: hydraulic
12) Servo Motor: AC2.9KW
13) Decoiling Motor:AC1.5KW
OPTION 2: Cassette change
Forming section / the cartridge fix on Cassette frame, for each profile changing
The entire forming cassette share in the same base frame
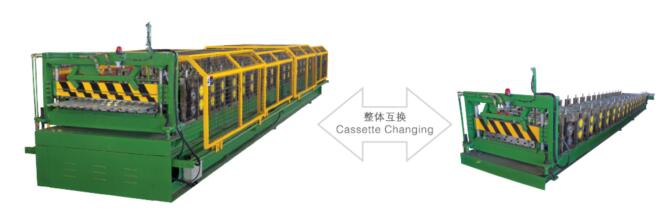
OPTION 3: Improvement for driving system
Driving system with gear box and redirector to improve the speed and tolerance control
Sprocket driving system between three/four stages
The below drawing and pictures are for your reference only

OPTION 4: Max. line speed of the roll former increased to 20m/min
|